沉管生产已于去年结束 记者 林桂炎 摄
【龙腾港珠澳】
海底隧道即将贯通,今起羊城晚报将推出报道,揭秘世界级难题解决的背后故事
记者林丹报道:港珠澳大桥海底隧道即将全线贯通,跨上了可以傲视“群桥”的最后一阶。即使再过120年,港珠澳大桥也足以令人致敬。
其实,一年多前,荷兰一家隧道工程咨询公司就举行过五星红旗升旗仪式,表达对中国港珠澳大桥岛隧建设者的敬意。这家“百年老店”在沉管隧道领域居于世界领先地位。而中国,在港珠澳大桥之前只做过几个长不过几百米的江河沉管隧道。当建设团队登上珠海牛头岛开建世界最大的沉管预制厂时,大家心里都还没底,不知如航母般巨大的沉管该怎么做。
荷兰公司的致敬是有理由的。港珠澳大桥被英国卫报评为“世界第七大奇迹”,实施过程中所遇困难都是世界性难题,而海上人工岛和海底沉管隧道又是其中难度最大的。尽管沉管隧道已有百年历史,但至今全世界也只有200来条沉管隧道。2000年以前,还没有一条3公里以上的隧道;2000年以后,北欧的厄勒隧道和韩国的釜山隧道也才3。51公里和3。24公里。
一分长一分险,实在是太难。港珠澳大桥的沉管隧道长6。7公里,几乎是厄勒隧道的两倍,也是世界规模最大的海底公路沉管隧道,更是世界范围内第一次尝试沉管深埋。做经典建筑理论,沉管隧道浅埋隧道,一般都在海床2-3米。但为了保证通行30万吨轮船,港珠澳大桥沉管隧道最大埋深近50米,也就是海床下30多米。这一“大”一“深”就带来诸多技术难题——
33节沉管,每节180米长、8万吨重,是迄今为止世界上最大体量的沉管。沉管越长,受力越大,预制的难度就越大。中国交建通过一系列的工艺创新,在世界范围内首次生产出高品质的混凝土自防水沉管,解决了超大型混凝土构件控裂难题,保证33节沉管共100多万平方米的混凝土毫无裂缝。要知道,全世界的沉管隧道漏水率平均值为10%,100%水密的隧道意味着什么样的挑战!
珠江口海域软土层厚度超过30米,这又让沉管沉降控制面临一大难关。通过一系列的世界首创,建设者们将沉管的沉降控制量从世界同类隧道的20厘米降低到10厘米以内;创新半刚性沉管结构出色地完成了沉管隧道深埋的超级挑战。
在外海条件下,将偌大的沉管从预制厂浮运到十多公里外的施工点,下沉到四五十米深的水下,将两个如中型航母般大的沉管精准对接,误差仅3毫米。如此庞大的身躯“相吻”,减少1毫米的误差在技术上都是一个飞跃,更何况珠江口变幻莫测的回淤,又提高了这道世界难题的难度分。
正因为难,能解题的高手全世界也就那么几个,这项技术被几个国家的专业公司垄断,要价过亿。中国的工程师们凭着一身本领攻下了这个关卡,研发出沉管沉放安装系统、泥沙回淤预警系统等数十个控制系统,解决了深水深槽、基槽回淤、珠江口特有的大径流等难题,形成了有知识产权的外海安装核心技术体系。
7年建设,7年创新。在岛隧工程建设中,创新比重前所未有地占总工程技术的15%,新技术创新64项,发明专利400多项。这些技术和创新迅速扩散到其他工程,两个人工岛的快速筑岛技术已在深中通道、三亚新机场的建设中使用。
预制厂里沉管生产线
最后一节沉管于去年底生产完成
“超级工程”港珠澳大桥催生“超级工厂”——世界最大的沉管预制厂
14个月荒岛变大厂 6年产超200万吨沉管
65年前,解放万山群岛的战斗,在珠海的桂山牛头岛打响。时隔超过一个甲子后,这座外海孤岛再次被广泛提及,是因为港珠澳大桥岛隧工程的巨型沉管在此预制。
2010年12月,岛隧工程桂山预制厂开建。在边勘察、边设计、边施工的“三边”紧急状况下,预制厂14个月内成功建成,厂房面积达56万平方米。随后的6年,33节平均达8万吨的沉管,相继从图纸走向工厂,由钢筋水泥变身“超级航母”。
这些构成沉管隧道基石的庞然大物,有着多个“最长”“唯一”“深海”等关键词,这也在过去几年一度成为“珠穆朗玛峰”级的工程难题。而中国建设者,以创造性的各式解决方案,攻克了这些世界性难点。中交港珠澳大桥岛隧工程总经理、总工程师林鸣表示:“这个拥有64项创新的工程,填补了多项技术空白。”
更难能可贵的是,港珠澳大桥岛隧项目创下一个工程佳话——截至目前,港珠澳大桥沉管隧道滴水不漏。在实现为港珠澳两岸三地“牵线搭桥”的同时,为海底隧道实现120年安全运营奠定坚实基础。
文/记者 马化展李国辉(除署名外) 图/记者 林桂炎
沉管预制经验几乎为零
与港珠澳大桥主体桥梁工程钢箱梁生产相似,岛隧工程的沉管也采用工厂法预制。在港珠澳大桥开建之前,世界上唯一一次使用过工厂法预制沉管并已建成大桥的,是在厄勒海峡隧道工程。但相比之下,港珠澳大桥沉管断面尺寸大,存在部分曲线管节,且是深埋式的,难度不可同日而语。
要建设33个标准管节平均长180米、宽37。95米、高11。4米、重约8万吨的沉管谈何容易?根据测算,每节沉管的排水量已超过“辽宁”号航母满载时的排水量,每个管节要消耗的钢筋(约7200吨)相当于搭建一座埃菲尔铁塔所需用钢量。
在工程筹备阶段,林鸣曾带队到正在建设巨加跨海大桥的韩国釜山,考察沉管基础施工专用设备,但施工单位只让他们在三四百米以外的海上匆匆看了一眼。
2010年,当得知要负责港珠澳大桥桂山沉管预制厂的设计任务时,中国交建集团的设计团队手头更是只有一本介绍性的英文参考文献,其中关于预制工厂的介绍不到30页。
但采用工厂法预制沉管是早就敲定下来的。港珠澳大桥120年的寿命要求,以及工厂法24小时可以连续生产,有限工期能够保证等优势,都注定它具备比干坞法预制更具可行性。
14个月荒岛变现代大厂
桂山预制厂,成了这一难题破解的最大见证者。
在此之前,沉管预制厂计划建在广州南沙,但如果选择南沙,每次运输沉管需要封航两天,而从珠海桂山牛头岛出发,可将浮运时间缩短至10个小时左右,至少能为珠江口往来船舶最繁忙的伶仃主航道“让路”一天。
桂山牛头岛是一个“四无荒岛”,无水、无电、无路、无通讯信号覆盖。选址调整使得沉管预制厂建设的工期变得更为紧张。沉管预制团队以焦虑的心情,边勘察、边设计、边施工。
“那是最艰苦的阶段,劳心劳力。”回忆起预制厂建设时期,港珠澳大桥岛隧项目Ⅲ工区二分区常务副经理陈伟彬感慨道,“有时设计刚出来,我们马上就得执行。”不过,这也恰恰是该项目的优势:设计和施工能无缝对接,工作得以紧锣密鼓推进。这也是国内在公路桥梁交通领域首次采用设计施工总承包管理模式。
最终,在这种既恶劣又紧急的环境下,1000多名建设者硬是用14个月的时间,于2012年2月建成了占地56万平方米的现代化沉管预制厂。这个世界级的超级工程,总爆破开挖量约200万立方米,混凝土浇筑量约为13万立方米,钢结构安装量达3000吨左右。
建成的沉管预制厂,拥有两条300多米长的流水生产线,集成了钢筋加工、钢筋笼绑扎和顶推、混凝土浇筑和养护、管节一次舾装、深浅坞蓄排水及管节起浮横移等全部工序。
用坏4台机器研制混凝土配方
过去一年,羊城晚报记者多次到桂山预制厂参观与采访。这里的沉管生产工艺已然非常成熟——平均每8天完成一道工序、每两个半月产出一节沉管,这是后期的标准生产节奏。
然而,2012年预制第一节沉管时,却用了7个月时间。和后期两个半月的生产时长比,这种变化并不是“熟能生巧”所能完整概括的。
以混凝土浇筑为例。早在沉管预制厂投产之前,沉管预制厂中心试验室就已率先启动,它承担为沉管找寻混凝土调配最佳配比的使命。不过,这项被沉管预制厂中心试验室主任张宝兰比喻为“寻找最佳口感米饭”的任务,并非一蹴而就的,因为要配置出最合适的混凝土,强度、耐久性、施工性、抗裂性各项指标都要全部符合需求。
张宝兰带领30余人的试验团队,通过将近一年的试验,反复验证各种配比,生产了100多吨混凝土,用坏了4个搅拌机,才研制出基础配方。随后又经过累计上百次调整、优化,“最佳口感的米饭”才算是做成了。
到了浇筑阶段,为实现从骨料堆放到混凝土入模的全程温度控制,多种温控技术被综合采用;为使3400立方米混凝土在30多个小时内一次性浇筑,300个关节支撑、100多楔形千斤顶的状况需经反复核查——这也是沉管预制工程高超技术水平和精湛管理水准的最佳注解。
56万平方米的沉管预制厂建在海外孤岛之上
构件误差在正负一毫米内
对岛隧工程沉管预制的要求,为何细致到几近苛求?陈伟彬的一番话或许可解答这一问题:桂山预制厂不像一般的工厂,允许存在一定的废品。我们的产品必须百分之百合格。作为一项要确保120年寿命的世纪工程,隧道安全大过天,而沉管生产质量是基础。
过去一段时间,记者采访了岛隧工程的总工程师、设计师、项目经理、技术员、工人等,发现他们中的多数人,都会主动提及“每一节沉管都是第一节沉管”这句话。而这种极度追求生产质量的业务态度,也直接反映在他们的工作之中。
这种对质量的严要求,使得这项制造沉管“航母”的任务,有时看起来更像是精细的手工活。比如,32种钢筋原材料要加工成330多种钢筋成品及其组合类型,每一个构件的误差都得在正负1毫米内;一个钢端壳设置了96个监测点,需在三天里不间断测量,以控制钢端壳的安装精度,从而保证沉管在深海里的密封止水效果。
而这也是林鸣向岛隧工程团队成员再三强调要求:“岛隧工程就像千人走钢丝,几千个人、几百道工序,容不得一丝纰漏。”
创新技术让沉管变“曲线”
每一步走得谨小慎微,不代表放弃创新。与此相反,生产的每一节沉管都注入了各种技术创新的元素。
根据港珠澳大桥岛隧工程设计总负责人刘晓东的测算,岛隧工程项目有50%是需要实验及突破界限的,其中与沉管生产相关的包括沉管基础、沉管预制等。截至目前,港珠澳大桥岛隧工程累计申报专利400多项,上报并经审批新工法7项。
曲线段沉管的成功预制,就是其中取得的一项突破成果。共计33节沉管中, E1至E28为直线段沉管, E29至E33为曲线段沉管,而大规模曲线段沉管工厂法预制,在全世界尚属首次。经过岛隧工程团队的多番研究论证,曲线段沉管采用“以折代曲”的施工工艺——将小节段预制成类似梯形的形状,达到与曲线相似的效果,第一个曲线段沉管早在2016年4月就已完成。
如今,沉管预制厂超额完成使命:浇筑100万方混凝土、沉管没有一条裂缝、设备没有发生一次故障、厂区实现一尘不染。在未来,港珠澳大桥沉管预制的成果,或将应用于深中通道、大连湾海底隧道等。它在为港珠澳大桥“筑通衢”的同时,也在为中国更多的工程项目树模板、立标杆。
揭秘
6.7公里沉管如何“滴水不漏”?
全长6.7公里、最深处超45米的海底隧道,其33节沉管的264个接头,毫无渗漏的痕迹。在这之中,沉管预制方面立下了哪些汗马功劳?
“混凝土秘方”的贡献自不待多言。沉管预制厂中心试验室团队通过长时间的试验,为沉管找寻到最合适的混凝土配比,使得完成浇筑的所有沉管混凝土本身没有任何裂缝。
这当然不是“滴水不漏”的全部原因。港珠澳大桥岛隧项目Ⅲ工区二分区常务副经理陈伟彬说,保证沉管滴水不漏,与预制的每一步骤都有关系。“原材料得确保检验到位,加工钢筋不能出现偏差,沉管顶推中一定不能发生变形”。
如果将沉管预制的所有步骤都计算在内,一共有156道工序。工作人员手头都有清晰的操作标准,这个名为《港珠澳大桥岛隧工程沉管预制质量控制点管理》的体系文件,包括6个大项、23个子项、116个小项。“不是一个人干得好就能让沉管‘滴水不漏’,而是要求桂山预制厂1000多人全都兢兢业业。”陈伟彬说。
“‘滴水不漏’还体现在管理的细节里。预制厂绝不会出现烟头,所有的设备都一尘不染。”三二工区副经理陈聪表示,“6S”现场管理(按时进行整理、整顿,及时做到清理、清扫,提高素养,保障安全),在桂山预制厂得到高标准推行,这也是保障施工质量的关键之一。
特写
在岛6年的老工人
喊来儿子同“战斗”
从2010年12月桂山预制厂开建至今,很多团队成员已在远离陆地的岛上工作将近7年。而随着沉管预制工作的完成,分别悄然而至,他们心里更多的是对这里的恋恋不舍。
来自湖北的黄青洲,于2011年初来到这座孤岛,参与桂山预制厂的建设,后来成为沉管预制机务班长。他表示,来时觉得六七年太长了,现在觉得过得太快了。
黄青洲有多爱桂山预制厂?过去几年,他把老婆、儿子、儿媳妇都介绍到这里来工作了。他觉得这里有人情味,吃、住等都比别的地方好。黄青洲还告诉后来负责吊运钢筋的儿子,要是在管理这样严格的地方都能做下去,以后到哪个工地都能上手。“即便现在沉管预制已经结束,这里的设备都会维护得很好,处于随时能用的状态”。
和黄青洲一样,工人们已经爱上这片此前从未听说过的土地以及这个世纪工程。沉管预制已经完毕,有些工人已离开了桂山牛头岛。“大部分人走的时候,都是非常留恋的。”有的工人回到老家,说起是在做港珠澳大桥工程时,村里老少都过来听他讲述经历。“等到大桥通车时,我想带着一家人去看看。看到我们参与建设的隧道通车时,会有别样的体验。”黄青洲说。
专访中交港珠澳大桥岛隧工程总经理、总工程师林鸣:
把港珠澳大桥当艺术品来做
“让子弹飞一会。”林鸣反复念叨这句话,或许这句话很好地诠释了这位中交港珠澳大桥岛隧工程总经理、总工程师内心对工匠精神、对极致的追求。
你会用个什么词来形容水泥墙?林鸣用“玉”!不,他不仅是形容,而是追求。在港珠澳大桥海底隧道的入口都有三道16米高、200米长的水泥墙,光滑如镜。再看牛头岛预制件厂的5万个小构件,精致如瓷。
要把巨大的土木工程当作艺术品来做,林鸣总是自己为难自己。
沉管深埋,世界性难题,没有先例。林鸣的团队用了近1年的时间反复研究论证,在希望和失望中度过一夜又一夜。灵感来自某天凌晨,但“半刚性”沉管的想法却备受质疑,内部担心“过度创新”带来风险,外国权威专家担心中国尚无能力“创造一个新的结构”。但林鸣坚持认为:“‘半刚性’是一种科学的解决办法,如果不坚持就没有尽到责任。”最终,6家专业机构的分析计算结果证明林鸣想法的可行。
“我能不能做得更好?”要知道,技术已到极限,再进一分都难。沉管沉降控制在30厘米是正常值,合同规定20厘米,已是难上加难。“我们为什么不再突破一下?”这股拗劲,让港珠澳大桥的沉管沉降控制在10厘米以内。
林鸣一直崇尚工匠精神、铁人精神和科学家精神。“工匠精神就是追求卓越,铁人精神是拼搏精神,科学家精神就是永无止境的探索。”从最初接受港珠澳大桥岛隧工程的任务到今天,林鸣团队的技术创新64项,获得发明专利400多项,而其中许多创新来自他们对蛛丝马迹的洞察。E20节沉管安装对接后的第20天,回淤突然猛增,此后每天回淤10厘米-20厘米。其实,沉管已成功对接,没有出现任何问题,林鸣对回淤完全可以视而不见。可他心里就是留不下一丝疑虑,“是不是我们判断有误?”他们立即开展了半年的纳淤机理实验,“证明我们以前的判断是错的,淤泥不是漂在表面的,基槽石头的空隙能容纳很多淤泥。”林鸣的问题又来了:“能不能在50米的水下把石头空隙的淤泥清了而不动石头呢?”这似乎是异想天开,全世界没有任何一项工程,没有任何一台机械可以在碎石间清淤的。上海振华重工用了4个月完成了这项“奇葩”任务——世界上第一台深水碎石基床整平船诞生,作业水深可达60米,清淤精度误差小于4厘米。
它甫一出生,任务就来了。E22节沉管回淤2000平方米,比以往任何一次都严重,深水碎石基床整平船上阵仅4天即凯旋。“这样的困难我们都能解决了,还有什么困难不能克服!”探索和解决难题对林鸣这样的有志者来说,是兴奋和愉悦。
林鸣常对他的团队说:“深埋沉管历史性地摆在中国工程师面前,我们不能在中国的超级工程上留下任何遗憾。”直到今天,他仍如履薄冰:“1米不通,一切都是零!”......查看原文:http://www.hellosea.net/news/focus/2017-04-17/40252.html
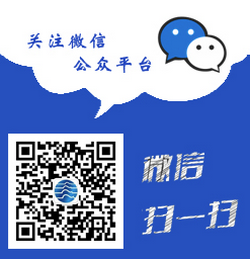
- 频道推荐
- 最新新闻